Jan 24.2022
Switching construction production mode to digital twin construction
The future of the construction sites is the constitution and integration of different technologies to produce both virtual and actual construction production processes that eliminate delivery time and costs, increase health and safety awareness, and improve production performance. This can be achieved with the adoption of digital building platforms within Architectural, Engineering, Construction and Operation (AECO) companies that have to adapt with the digital swift and produce assets and services in a more comprehensive, efficient and effective way.??
Facts?
What if as a building contractor were you able to have zero accidents, improve labour productivity by 30% and zero carbon neutrality? What if your project could build up faster, gain reputation faster and improved Return of Investment (ROI) could have more chances to be reached? Would you start collecting construction project data to help you meet these targets? The volume of data is produced, shared and impact the construction building process is terabyte and its value can save $0.7-1.2 trillion (13- 21%) in the Design & Engineering and Construction phases and $0.3-0.5 trillion (10-17%) in the Operations phase according to World Economic Forum. 95% of all data captured in the construction and engineering industry goes unused. Many projects are under pressure to progress because of cash flow challenges during the construction building process! So, having a smart construction site could really help these challenges?
Switch construction production mode: From physical construction to digital twin construction
In traditional engineering construction, each stage of the project is relatively fragmented and less collaborative. In fact, the feasibility of construction and the implementation of the operational and maintenance stage results in many large numbers of reworks, delays and cost over-control. In the digital era, every house "is twice built" in the future, which means to perform virtual construction of full-digitalisation first and then perform physical construction of industrialisation. During the virtual construction, all participants work together on the digital building platform to conduct digital proofing of the lifecycle process from intelligent design to virtual production, construction, and operational and maintenance. As a result, the team delivers a full-digital sample of optimal design scheme, feasible implementation scheme and reasonable business scheme. Then, through construction upgrade based on the digital twin to lean construction with planned construction processes, industrial-based physical buildings are built in the physical world to minimise project waste, maximise project value, and upgrade the construction to modern upgraded construction.
Figure 1?Transformation of Production Mode from Physical Construction to Digital Twin Construction
Can the new construction production mode add value to my business?
The new construction production mode that empowers the integration of different technologies during the construction building process enables (real-time) data-driven decisions. In fact, it can help to tackle some core challenges that exist in construction sites, such as skills shortages, health and safety, technology adoption and worker productivity. The power of acquiring the right and accurate data from a construction site during the building process could unlock the global construction industry by allowing faster completion of projects by meeting its KPIs. Moreover, the fast growth of Internet penetration increases the production and utilization of terminals such as tablets, smartphones, laptops etc. Certainly, though due to the low number of digital–led skilled workforce accessibility and affordability of the above technologies is becoming relatively easier. However due to the increase of digital transformation within enterprises, we see 30.8% of contractors do not bid on projects involving BIM; 36% of construction professions stated that current technologies are not integrated into existing construction processes and procedures, while 38.2% of construction firms cite "lack of staff to support the technology" as a primary limiting factor to adopting new?technology. Meanwhile, according to the same report, 28% of UK construction firms say that lacking the information they need on-site is the single biggest factor impacting their productivity. 59% of companies state that their workforce doesn't have the skills needed to work with BIM. 70% of contractors in the USA believe that advanced technologies can increase productivity (78%), improve schedule (75%), and enhance safety (79%). Moreover, technologies like AI have the potential to increase the construction industry's profits by 71% by 2035 and are forecasted to reach $4.51 billion by 2026 in the?construction industry. Hence, building contractors should be looking for smart solutions to increase site productivity, efficiency, green operation, and safety but at the same time to increase their ROI and meet clients' requirements. By taking a more innovative and integrated approach, building companies can gain great value from new integrated construction site strategies and their solutions by improving delivery efficiency by using Digital Building Platforms.
Empower through Digital Building Platforms?
Digital building platform is the web-based platform of the building industry, which integrates cutting-edge digital technology and advanced lean construction theory and method. The digital building platform run through the process project lifecycle (figure 2), upgrade the industry throughout, connect projects' stakeholders by providing virtual construction and digital twin construction services, systematically develop optimal allocation of resources in the whole industry chain, maximise production efficiency, and empower all supply chain stakeholders to achieve the industrial goal of making every project successful. As the digital infrastructure of industrial digital transformation, the digital building platform build a "digital base" for the industry to a) lead the digital twin world, b) build a "digital production line" with software and data, and c) implement intelligent project management based on the "brain of project" of "data and algorithms".
Figure 2?Business Architecture of Digital Building Platform
Develop digital twin construction for virtual control
The integrated "digital production line", which integrates factory production and on-site construction, drives factory lean production with on-site lean construction and develops the automation of intelligent production scheduling, logistics scheduling, construction scheduling, and other data flow. In the "physical production line", the real-time capturing, analysis, decision-making, intelligent construction visualisation of personnel, machinery, materials, and other elements are developed through the digital twinning of the digital construction and physical construction site. Finally, the integration of the factory and site is formed.
Create digital twin construction services
New physical construction service providers, the creators and final deliverers of construction products, provide digital virtual construction services and industrial physical construction services for owners. Based on the digital building platform, the new physical construction service providers develop both the "soft power" of whole-process lean management of projects, and the "hard power" of digital twin construction services. In terms of production mode, projects are built and delivered based on "two production lines", as shown in figure 3. One is a digital production line featured by digital intelligence, and the other is a physical production line featured by automation. The digital building platform provides efficient allocation of resources by offering "two construction" services. These are consist of a) full-digital virtual construction that delivers intelligent design and supply & procurement, virtual production/construction/O&M, and b) digital twin physical construction that delivers procurement, industrial production and lean construction. As a result, two building products are handed over to the owner: the digital virtual building and the physical building.
Figure 3 New Construction Service Providers Build Two Production Lines
Summary
The emergence of new roles in the industry such as new physical construction service providers reshapes the division of work in the industrial ecosystem and creates industrial conditions for the upgrade of the industrial roles such as developers and production suppliers. Among others, developers upgrade from product developers to new operation service providers and provide various services for building space concerns. Moreover, traditional production suppliers grow into new production service providers that limit their production to marketability with the empowerment of the digital building platform.
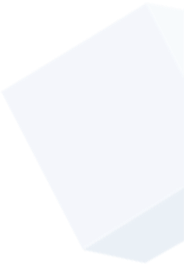