Nov 18.2019
Empowering the Industry with Digital Building: How We Build in the Future
After its development and practice over recent years, the concept of digital building has been widely recognized by the industry and is propelling the digital transformation of the industry as a new driving force. As a guiding development strategy of the industry, digital building also outlines the work scenarios of the industry in the future. The Digital Building: White Paper on the Digital Transformation of the Construction Industry ?released in June this year systematically explains how to build houses in the future. This article summarizes ? the key ideas and scenarios provided in the White Paper, so that readers can have a more vivid perception of the promising future of the construction industry in the digital age.
New visions into the future of the construction industry
As China emphasizes
?quality instead of speed in its economic growth, the construction industry, one of the pillars that have empowered the national economy, also encounters new opportunities and challenges. Construction projects, being the pivot of the production and operation activities of a construction enterprise, play a vital role in determining the health and growth of the construction enterprise, and affect the direction of industrial transformation and upgrading. Making every project successful is therefore of crucial significance. The success of a project should cover the full life cycle of building, including not only the product but also the construction process of the project.
1. High-quality building products
Statistics show that humans spend about 4/5 of their time in buildings, and architectural space provides people with an environment to live and work. That’s why the quality of building products matters a lot for improving the quality of life and work. Empowered by the digital building platform, building products that meet personalized customization requirements, have industrial-grade quality, and are human-centered will definitely win the future.
Personalized customization: Unlike the delivery mode of traditional building products, the new product development mode features user participation and large-scale personalized customization. Thanks to the digital building platform, users are able to participate in the design and type selection of buildings and introduce personalized elements. This user-centered feature ensures flexible production and delivery of personalized customization in living or working spaces.
Industrial-grade quality: Construction of buildings is driven by data. Digitized design, factory processing, mechanized installation, and integrated decoration all help achieve a higher quality of building products that are comparable to that of other industrial products such as mobile phones and automobiles. For example, the buildings of Apple Park are great demonstrations of industrial-grade quality. During the construction of the building, the error of the glass curtain wall was controlled within 0.88 mm.
Healthy building space: To take care of human health, digital technology is applied in the design stage to simulate and optimize the building space; in the operation and maintenance stage, the building can sense the built environment both inside and outside it in real-time, and automatically adjust the status of equipment in the building to keep people in a healthy and comfortable living and working environment.
2. Lean construction process
The success of construction projects and the achievement of industrial goals not only bring considerable economic benefits to construction enterprises and evolve the construction industry, but they also have the following significant economic and social benefits in promoting the development of green and compact communities.
The construction cost is reduced by 1/3. High cost is the reason for the low-profit margin of most construction enterprises. Reduction of the project cost by 1/3 will give a drastic rise in their profit. As for society, such cost reduction means less waste of materials and labor force, and lower consumption of resources.
The carbon dioxide emission is reduced by 50%. This implies an immense benefit to the environment of our country and the rest of the world. Data shows that more than 40% of China’s carbon emissions come from the construction industry, and China’s carbon dioxide emissions are among the highest in the world. Apparently, if we can reduce the carbon dioxide emissions in the construction industry, we will have a bluer sky, cleaner air, and a better urban environment.
The construction progress is 50% faster. For the Developer, speeding up the construction progress is to reduce the project cost. Construction projects are getting bigger today, requiring a larger amount of funds but at a higher fundraising cost. Speeding up the progress help withdraw funds quickly and obtain more investment benefits. For the general public, faster project progress means a shorter construction period and less interference to the community. People's lives will be more convenient.
Zero quality defect. For the Developer, delivering a building product of industrial-grade quality is key to meeting people’s higher consumer expectations and improving customer satisfaction. For society, green, healthy and smart high-quality building products not only satisfy people's requirements of a better living and working environment but also an important embodiment of our vision of a beautiful China.
Zero safety accident. Construction is a high-risk industry. Its annual casualties due to safety accidents have been higher than that of other industries. The practice of the zero-accident approach has a substantial significance in improving the occupational environment and productivity of the construction industry.
3. New driving force for upgrading the industry
Delivering successful building products through a lean construction process has been a shared vision in the industry. To achieve it, most will opt for a development model that is driven by digital technological innovations, and digital building platforms will be a new driving force for upgrading the industry. A digital building platform is an internet-based platform for the construction industry. It leverages BIM, cloud computing, big data, IoT, mobile Internet, AI and other information technologies to digitize all factors and participants in the whole construction process for intelligent online management. It is built on the advanced lean construction theories and methods and integrates personnel, process, data, technology and business system.
The digital building platform enables construction enterprises to design and construct their projects in the digital world, and then build brick-and-mortar buildings in the physical world. This huge transformation from the traditional construction model can bring the digital construction capabilities of the entire industry chain to another level, promoting China from a "big builder" to a world power of strongly competitive construction technology.
Thanks to the digital building platform, we are able to apply the digital technology in the construction industry and build a new type of digital infrastructure that fully interconnects workers, machines, materials, methods, and environment, and realizes the linkage, complementarity and efficient arrangement of all factors and participants in the whole construction process. A new industrial ecosystem is taking shape with the support of the platform. Digital twin, data-driven, open, and intelligence-dominant are the basic characteristics of the digital building platform.
Digital twin. With the help of Cyber Physical System (CPS), buildings, all factors and participants in the whole construction process of a project are digitized online to create a corresponding virtual model, which is a digital twin of the physical project that coexists in cyberspace. This digital twin is used to simulate the behavior of physical entities in the real world, so as to add up new capabilities to them based on the feedback from the virtual model, data fusion analysis and decision-making, and iterative optimization. The productivity, management efficiency and decision-making ability are therefore improved.
Data-driven. Optimal allocation of production factors and resources is driven by data. As the Internet of Everything continues to develop, almost all production equipment, sensing devices, networking terminals and even producers are generating data constantly. In fact, data has become a new type of asset, resource, and production factor. Data streams carrying information and knowledge flow freely along the chain of value and realizes the optimal allocation of resources while flowing automatically in the closed-loop of data.
The power of openness. The digital building platform ensures that numerous stakeholders in the industrial chain come together to form an ecosystem, where they can jointly complete the design, procurement, production, construction, and operation and maintenance of projects, shaping a competitive and powerful industrial cluster. Moreover, the platform can realize "vertical integration of industrial chain, horizontal integration of value chain, and end-to-end connection". The direct and the indirect industrial chains can be associated, and an open, shared, and clustered industrial ecosystem can be formed.
Intelligence-dominated. By deepening the application of big data, AI and other cutting-edge technologies in the design, procurement, production, construction, operation and maintenance of projects, we can build an intelligent data-driven closed-loop empowerment system for status perception, real-time analysis, scientific decision-making, and precise execution. In this way, we can gradually develop an intelligent operating system that can eventually manage the entire process of the whole project that engages the industrial ecosystem.
Something new about the buildings in the future
Empowered by the digital building concept, some new features will be introduced to the construction industry. On the demand side, consumers will be able to personalize their homes through digital platforms instead of being offered with standardized predefined houses; on the supply side, construction enterprises will construct the same building "twice", virtually first and then physically built, first in the factory and then on the smart site, and deliver two versions of the building, one virtual and one physical.
Large-scale personalized customization. Consumers are able to customize their own homes. When buying a house, consumers can use the digital platform to flexibly combine and adjust different living spaces. They can also select different styles of furniture and materials from the digital warehouse, and visually configure the "soft" and "hard" decorations. After that, they can analyze and evaluate the environmental conditions of the space on the platform and get a plan that meets the health requirements. At last, they can use VR and AR virtual reality technology to have an immersive experience in their personalized space. This mode has been realized in the project we cooperated with Jingrui Real Estate. Currently, the platform provides more than 226 categories of items, and 75% of buyers have made their selections.
In the future, a building will be constructed twice. The construction enterprise will first complete a digital version of the building, refine it, and then construct it with bricks and mortar in a lean construction process. During the virtual construction, all parties of the project work together on the digital building platform to verify the entire process from collaborative design to virtual production, construction and operation and maintenance, so as to deliver a digital sample that has the best design plan, feasible implementation plan, and reasonable business plan. After its digital twin is verified, the lean construction of a physical building can be ensured. By applying delicacy management to schedule tasks from the bottom level with time being accurately specified to the hour (or even minutes), indicate every execution process of tasks, and refine the "drawing model" to the component level, we can minimize the waste and maximize the value of the project, and deliver industrial-grade quality building products.
Buildings will be "fabricated in the factory and constructed on-site". The factory and construction site are integrated to build "two production lines", one digital and the other physical, and realize two "automation", i.e. the visible automation of production equipment, and the other is invisible automation of data flow. By leveraging the "digital production line" that integrates factory production and on-site construction, we can fully engage the factory and the construction site, and drive the industrial production at the factory with on-site industrial construction, so as to realize intelligent scheduling of production, logistics, and construction based on the automation of data flow. As to the physical production line, we can use the digital site, i.e. the digital twin of the physical site, to realize real-time identification, analysis, decision-making and intelligent execution of all production factors, including workers, machines, and materials, making it a "smart site". By introducing advanced production equipment such as CNC ( computerized numerical control ), machine tools and robotic manipulator arms, we chan realize automatic and flexible production.
The "automation" of the future construction sites. Relying on the digital building platform, which functions as the "brain" of the project, we can make use of cloud and edge computing technology to drive on-site operation with data and algorithms. Under the remote monitoring and control of managers, on-site robots and drones scan site conditions for modeling and carry out on-site operations. The entire process is driven by digital models. The automation of the construction site can greatly improve productivity and effectively prevent quality defects of on-site tasks and safety accidents.
Two "buildings" are delivered upon the project completion. During the completion phase, construction enterprises will deliver two "buildings" to consumers, one brick-and-mortar building and its virtual digital twin. The virtual digital building not only enables us to trace all information and data during the construction of the project at any time but also provides information model and data support for subsequent intelligent operation and maintenance of the building, ensuring the healthy operation and effective use of the building throughout its full life cycle.
Conclusion
As the blueprint for the construction industry in the digital age becomes clear, this article focuses on how to construct buildings in the future, and systematically describes the new features of the construction industry brought about by the digital building concept. We believe that the digital building concept will spawn more intelligent applications soon and support the construction industry to achieve higher quality. The future can be expected and let's join hands to work for it!
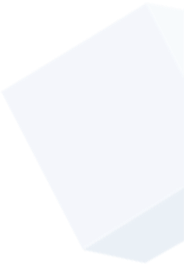